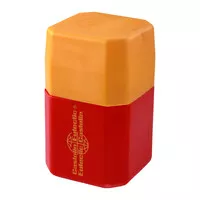
RotoTec CoroResist 19300 metal powder
355,86 € 237,24 € / kgfor corrosion-resistant coatings

Eutalloy RW 12112 metal powder mixture
2.648,07 € 529,61 € / kgfor wear-resistant coatings

MetaCeram 28010 Ceramic powder
931,50 € 776,25 € / kgCeramic powder for wear- and corrosio...
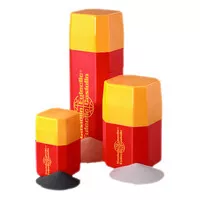
RotoTec HardTec 19400 metalic powder
365,33 € 270,61 € / kgfor adhesion-resistant coatings

MetaCeram 28030 Ceramic powder
349,27 € 291,06 € / kgCeramic powder for wear- and corrosio...

Eutalloy RW 12494
1.389,04 € 347,26 € / kgMetal powder for heat-resistant coatings
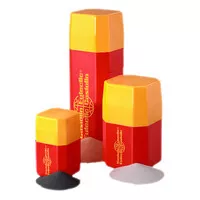
RotoTec FrixTec 19850 metal powder
593,28 € 439,47 € / kgfor adhesion-resistant coatings
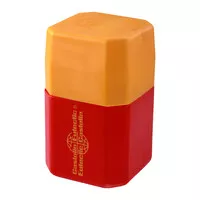
RotoTec LubroTec 19985 Metal powder
635,42 € 470,68 € / kgfor machinable coatings

Eutalloy RW 12495
1.384,17 € 346,04 € / kgMetal powder for heat-resistant coatings
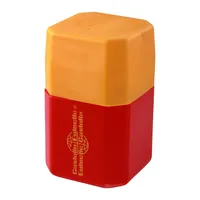
RotoTec DuroTec 19910
489,33 € 362,47 € / kgMetal powder for wear-resistant coatings

SuperJet -S- Eutalloy powder flame sprayers
1.695,20 €Powder flame spraying
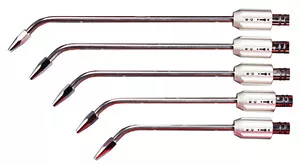
Burner tube with nozzle
267,66 €for SuperJet-S-Eutalloy

CastoDyn DS 8000 flame spraying system
5.841,83 €Advanced flame spraying system

Standard spray module for thermal spraying
715,15 €for CastoDyn DS 8000

Eutalloy 15999 Metal powder
385,41 € 550,59 € / kgfor wear-resistant coatings

Eutalloy PE 8418 metal powder
414,19 € 82,84 € / kgfor coatings and repairs of glass molds

Eutalloy 10911 Metal powder mixture
580,08 € 116,02 € / kgfor wear-resistant coatings

Eutalloy BoroTec 10009 metal powder
312,58 € 446,54 € / kgfor abrasion-resistant coatings

Eutalloy NiTec 10224 metal powder
320,37 € 457,67 € / kgfor cast iron materials

Eutalloy TungTec 10112 Metal powder mixture
382,36 € 546,23 € / kgfor extremely wear-resistant coatings

Eutalloy UltrAloy 10611 Metal powder mixture
381,36 € 544,80 € / kgfor wear and heat-resistant coatings

Eutalloy RW 12496 Metal powder
1.366,06 € 341,52 € / kgfor hot wear resistant coatings

Eutalloy RW 12999 metal powder mixture
949,50 € 189,90 € / kgfor highly wear-resistant coatings

ProXon 21021 metal powder
448,79 € 359,03 € / kgfor primer coats

ProXon 21031 Metal powder
776,32 € 310,53 € / kgfor adhesion-resistant coatings

ProXon 21071 metal powder
396,19 € 316,95 € / kgfor adhesion-resistant coatings

MetaCeram 28060 Ceramic powder
226,60 € 188,83 € / kgCeramic powder for wear-resistant coa...

MetaCeram 28085 Ceramic powder
717,30 € 143,46 € / kgCeramic powder for high-temperature c...

MetaCeram 28095 metal powder
414,44 €for adhesion-resistant coatings

Eutalloy ChromTec 10680 metal powder
295,82 € 422,60 € / kgfor wear-resistant coatings

Eutalloy 8426 PE powder
400,27 € 80,05 € / kgSelf fluxing nickel-base alloy

Eutalloy PE 8422 Self fluxing nickel-base alloy
448,01 € 89,60 € / kgSelf-fluxing nickel-base alloy

Eutalloy PE 8431
366,89 €Self-flowing metal powder for coating...

Eutalloy PE 8435
405,96 €Self-flowing metal powder for powder ...

Eutalloy PE 8440
423,78 € 84,76 € / kgSelf-flowing metal powder for powder ...

CobalTec 10092
442,54 € 632,20 € / kgMetal powder for corrosion-resistant ...

Eutalloy 10185
366,19 € 523,13 € / kgMetal powder for adhesion-resistant c...
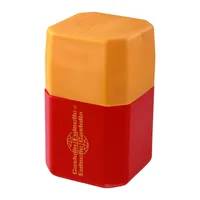
RotoTec 29230 LT - Metal powder
135,05 € 100,04 € / kgfor corrosion-resistant coatings

Eutalloy RW 12525 metal powder
725,53 € 145,11 € / kgMetal powder for corrosion and wear-r...
SuperJet S, handle
1.185,86 €for SuperJet S Eutalloy
RotoGuard (90111)
88,66 € 110,82 € / kgSealant for sealing spray coatings
Nozzle coated
54,66 €for SuperJet S Eutalloy
Thermal spraying is a coating process in which a coating material in wire or powder form is melted or fused by applying thermal energy and accelerated by a gas flow in the direction of a component surface to be coated. In contrast to welding, the base material is not melted. Adhesion is mainly achieved by mechanical interlocking in superposition with induced shrinkage stresses. Residual stresses and metallurgical interactions as well as diffusion processes and van der Waals forces also influence the layer adhesion.
The substrate must be roughened in a previous work step so that a form fit can occur between the spray particles and the substrate. The particles then cling to the generated roughness peaks. Roughening is usually done by sandblasting, but can also be done by high-pressure water jets or mechanically (turning, milling, grinding).
Castolin Eutectic products are highly regarded for quality and reliability by experts in various industries worldwide. Our range includes spray guns, welding equipment, wire feeders and accessories for efficient and cost-effective projects.
Thermal spray is a breakthrough technology that is redefining surface coating and refurbishment processes in various sectors. A material is heated at high temperature, melted and sprayed onto a surface. There it solidifies and creates a versatile coating with properties such as wear and corrosion resistance as well as thermal insulation.
This innovative method allows various materials to be applied to a target surface. The result is a robust, protective layer that increases the performance and service life of components. The heat source in thermal spraying melts or softens the coating material, which is then applied via a spray gun.
The heat source can be a flame, an electric arc or a plasma jet, depending on the specific spraying process. As soon as the molten or partially molten particles reach the surface, they harden and form a strongly adhesive protective layer.
Thermal spraying is very flexible and can work with different materials, for example metals, ceramics or plastics. These materials can be tailored to meet specific requirements such as corrosion resistance, wear resistance, thermal insulation, electrical conductivity or even aesthetic improvements.
Thanks to the wide range of coating materials, thermal spraying is suitable for many applications. It is used in industries such as aerospace, automotive, energy and manufacturing.
One of the main advantages of thermal spraying is the ability to create coatings of exceptional thickness. This ability allows for the restoration of worn or damaged components by building up the coating to its original dimensions. In addition, customized coatings can be produced with specific thicknesses that offer enhanced protection and performance characteristics.
Thermal spray coatings are known for their exceptional bond strength and durability. The rapid impact of molten particles ensures strong mechanical adhesion. As a result, the coatings are extremely temperature and environmentally resistant and can withstand demanding conditions. These coatings effectively protect against wear, corrosion and erosion, and increase the service life of components.
Thermal spraying is flexible and offers various methods such as flame spraying, arc spraying, plasma spraying and HVOF (high velocity oxygen fuel spraying).
Each method has its advantages. The choice depends on things like the material of the coating, the type of substrate, the thickness of the coating and the desired result.
This versatility allows precise control of the coating process and ensures optimal results for a wide range of applications.
In addition, thermally sprayed coatings can be post-treated or finished to further improve their properties. Additional treatments such as grinding, polishing or milling can be used for specific surfaces, dimensional accuracy or appearance.
The variety of customization and post-treatment options makes thermal coatings extremely flexible for individual application needs.