Contact
- +32 2888 2451
- info@castolin.be
- shop.castolin.com
S.a. Castolin Benelux n.v.
Werkplaatsenstraat / Rue des Ateliers 11
7850 Edingen / Enghien
Belgium
VAT: BE0402932258
Availability
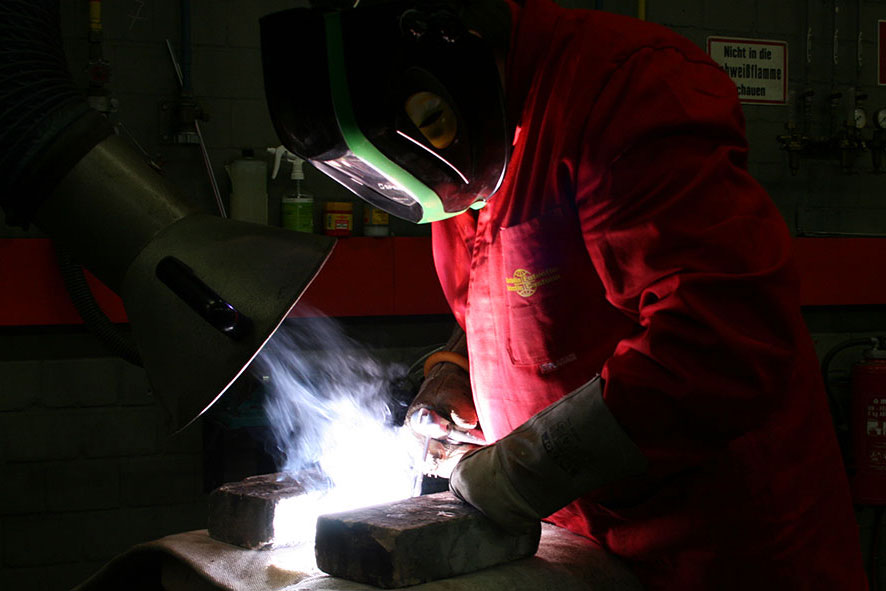
Cast iron is an essential material in various industries, prized for its strength, durability, and machinability. Despite its robust nature, cast iron components can fail due to wear, stress, or improper handling. Repairing cast iron requires a specialized approach to ensure durability and reliability. In this guide, we’ll outline the critical steps and best practices for effectively repairing cast iron parts.
Contents
- Understanding Cast Iron and Its Types
- Challenges in Cast Iron Repair
- Step-by-Step Repair Process
- Key Welding Techniques
- Final Considerations
1. Understanding cast iron and its types
Cast iron is an alloy of iron, carbon, and silicon, known for its exceptional machinability, high compressive strength, and vibration-damping properties. However, its brittleness can pose challenges during repair. Common types of cast iron include:
- Gray Cast Iron: Characterized by its graphite flakes, offering good thermal conductivity but lower tensile strength.
- Ductile iron: Graphite in nodular form provides enhanced ductility and toughness.
- White iron: High hardness but poor weldability due to its carbides.
- Malleable iron: Improved ductility through heat treatment.
Each type has specific properties that influence its repair process, from weldability to thermal management.
2. Challenges in cast iron repair
Repairing cast iron involves overcoming several challenges:
- Brittleness: Cast iron’s tendency to crack under stress requires careful handling.
- Heat sensitivity: Improper heating can lead to the formation of brittle phases like cementite and martensite.
- Material variability: Different grades and types of cast iron respond differently to welding and repair techniques.
Addressing these challenges requires a methodical approach, from proper material identification to selecting the right repair alloy.
3. Step-by-step repair process
Repairing cast iron involves the following seven steps:
Step 1: Prepare the defective area
- Remove the damaged section using grinding or a tungsten carbide burr.
- If using arc-air removal, preheat to 287.8–315.6°C to avoid brittle structures.
Step 2: Clean the weld zone
Lightly grind the area after arc-gouging to eliminate hardened material.
Step 3: Preheat the component
- Refer to the preheating guidelines:
- Gray Iron: 287.8–315.6°C
- Ductile Iron: 93.3–148.9°C (ferritic) or 287.8–329.4°C (pearlitic)
Step 4: Apply a butter layer
Butter the joint with a compatible repair alloy to reduce stress concentration.
Step 5: Peen the weld metal
Hot peening minimizes contractional stresses and improves toughness.
Step 6: Select the correct filler metal
Choose a filler with properties that match the casting, ensuring strength and machinability.
Step 7: Cool slowly
Allow the part to cool gradually to room temperature, avoiding quenching to prevent residual stress cracks.
4. Key welding techniques
Cold welding cast iron - dissimilar metals
The cold welding cast iron procedure requires no preheat and a dissimilar metal welding alloy. The casting should be hand-warm and free from moisture or condensate in the area of the welding zone. It is welded using the stringer bead technique plus peening. The cold welding procedure is always recommended when:
• warping or a distortion of the parts and components to be processed is not acceptable;
• the casting cannot be preheated due to its size or geometry;
• preheating equipment is unsuitable or not available.
Hot welding cast iron - similar metals
The hot welding cast iron procedure requires slow preheating of the complete casting to between 287°C and 315°C after a suitable welding zone preparation. Then a postweld heat treatment (PWHT) according to the base metal, is applied. The hot welding procedure is always recommended when:
- the mechanical properties, machinability, or color of the weld deposit must closely correspond to those of the casting;
- the cast workpiece can be positioned and welded while it is located in a gas-fired or electrical brick furnace;
- warping, distortion, or surface oxidation can be accepted up to a certain degree.
Repair alloys
- Examples of repair alloys:
- EutecTrode® 2-24
- EutecTrode XHD 2230
- EnDOtec DO*23
5. Final considerations
When repairing cast iron, it’s essential to:
- Understand the specific grade and properties of the casting.
- Follow tested guidelines for welding and post-repair handling.
- Choose repair alloys and techniques tailored to the application.
By adhering to these practices, you can effectively restore cast iron components, ensuring their longevity and reliability in demanding industrial environments.
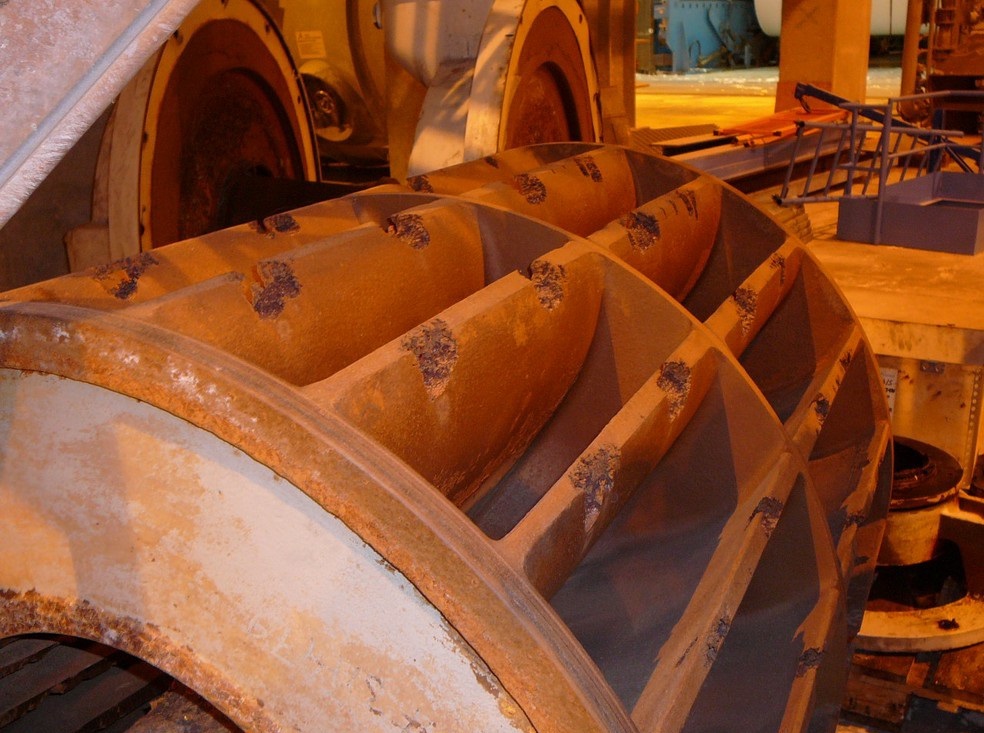