- All products
- TIG torch Welding torch
- TIG torches - Accessories
- MIG/MAG torch
- MIG/MAG torches - accessories
MIG/MAG torches are essential tools for welders who need reliable and efficient welding performance. These torches are available in various sizes and power levels to meet the requirements of different welding tasks. There are different types of MIG/MAG torches, including standard MIG/MAG torches, water-cooled MIG/MAG torches and gas nozzle MIG/MAG torches. Each type of torch has its own advantages and is suitable for different applications.
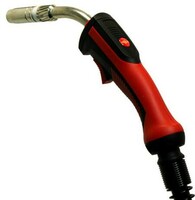
CastoPlus 256G MIG/MAG torch
73,41 £Gas-cooled MIG/MAG torch

CastoPlus 366G MIG/MAG torch
123,95 £Gas-cooled MIG/MAG torch
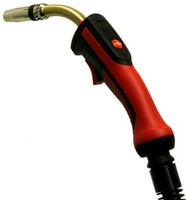
CastoPlus 306W MIG/MAG torch
221,48 £Water-cooled MIG/MAG torch
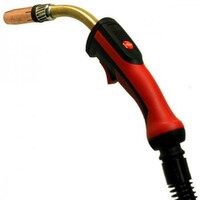
CastoPlus 506W MIG/MAG torch
191,71 £Water-cooled MIG/MAG torch
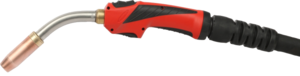
CastoPlus 3200iW U/D MIG/MAG torch
590,98 £Water-cooled MIG/MAG torch
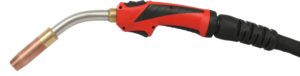
CASTOPLUS 5000iW U/D burner
607,32 £Water-cooled MIG/MAG torch
MIG/MAG torches are an essential part of MIG/MAG welding and can have a significant impact on the quality of the weld. These versatile and reliable tools facilitate the smooth and efficient fusion of metal, providing welders with unrivaled control and ease of use. The following explains the unique features and benefits of MIG/MAG torches and highlights their indispensable role in welding applications.
MIG/MAG torches are typically made of metal and have a long, flexible cable that connects to the welding machine. The cable is equipped with a wire feed mechanism that feeds the welding wire into the torch. The torch also has a contact tip that touches the workpiece and a nozzle that feeds the shielding gas into the welding area.
MIG/MAG torches are known for their precise and consistent wire feed mechanisms. They work with reliable wire drive systems that ensure even and continuous wire feed, promoting stable arc characteristics and optimum weld quality. Welders can adjust the wire feed speed to achieve precise deposition rate control, ensuring accurate placement of weld beads and achieving the desired results effortlessly.
The shielding gas supply system of the MIG/MAG torches is designed to ensure effective protection of the weld pool. The gas nozzle and diffuser work together to deliver an even flow of shielding gas around the welding area, preventing atmospheric contamination and ensuring clean, high quality welds. The welder can easily adjust the gas flow rate and angle for optimum coverage, resulting in an excellent weld bead appearance and improved weld quality.
The MIG/MAG torches are designed for durability and longevity in demanding welding environments. They are characterized by a robust construction with high-quality materials that can withstand the harsh conditions of daily use. Heat-resistant components, such as heat-resistant cables and insulated handles, protect the torch from excessive heat and extend its service life. This durability ensures consistent performance and reduces the need to replace the torch frequently, minimizing downtime and maintenance costs.
A key benefit of MIG/MAG torches is the ease of maintenance. They are designed for quick and convenient cleaning and replacement of wearing parts. Contact tips, gas nozzles and diffusers are easily accessible and can be replaced, ensuring optimal performance and minimizing downtime. Thanks to this streamlined maintenance process, welders can focus more on their welding tasks and less on maintaining the equipment, maximizing productivity.
Safety is a top priority in welding operations and MIG/MAG torches have various safety features to protect the welder and the environment. The torches are often equipped with built-in mechanisms that prevent accidental triggering or gas flow, ensuring safe operation. In addition, it is important that welders wear appropriate personal protective equipment (PPE) such as welding gloves, safety goggles and flameproof clothing to protect themselves from heat, sparks and UV radiation.